LATEST NEWS Humans are at the heart of Nissan’s future factories
February 12, 2020
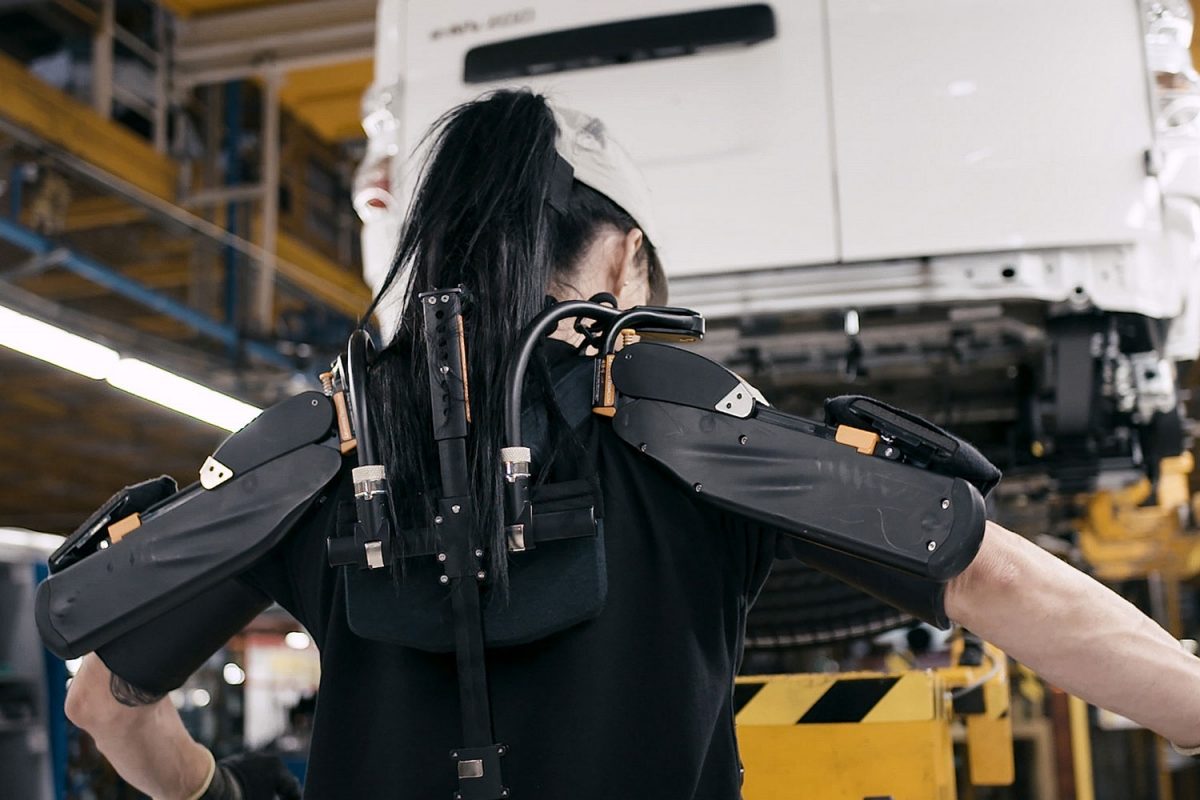
Ergonomics and technology are enabling humans and robots alike to play to their strengths
As Nissan prepares to build a new generation of electrified, intelligent and connected cars, the company is making a series of investments to upgrade its production technologies and facilities.
At first glance, these investments in automation and robotics might suggest that the factory of the future will be the exclusive domain of machines, not people. In fact, nothing could be further from the truth: manufacturing is as reliant on human beings as ever, and technology will serve to enhance their work.
This is because Nissan aims to do more than simply maximize output over a given period of time. We see efficiency in terms of preventing mistakes, maintaining quality, ensuring that workers are freed from monotonous tasks, and reducing strain and fatigue from work.
Entire engineering teams at Nissan are dedicated to studying ergonomics. For every process, they analyze the physical burden of certain actions (such as lifting, reaching, twisting or crouching) or the mental burden of tasks that are repetitive or require constant concentration. They then pick the most burdensome processes and come up with solutions to make life easier.
Here are just a few examples of how Nissan is assisting human workers as they bring the latest vehicles to life.
Choosing when to automate
Certain assembly line processes are best suited for robots, particularly if they’re simple and repetitive yet relatively strenuous for humans.
[https://flixel.com/cinemagraph/uyo7d2y40yww4aplenjo]
One example is the installation of a headliner, the overhead layer of material on the inside of a car’s roof. Ordinarily, workers must enter each vehicle’s cabin to perform this physically demanding job. The task has become even harder as cars come with more connected features, adding to the number of devices in and around the headliners.
Nissan’s solution is to use robots to insert the headliner through the front of the vehicle and then fasten it.
“Headliner installation is a physically demanding job, and it’s getting more difficult,” notes Nissan’s Kouji Abe, who worked on the new automated process. “Automation took years of development and testing, but hopefully we can now shift people to roles that can benefit the most from human expertise.”
Automation is also enhancing the quality control process, benefiting customers. Inspection staff at Nissan’s plants in Japan can pass or fail vehicles by simply speaking into a microphone connected to a voice recognition system. The results and other data are automatically logged, eliminating not only mistakes but also cumbersome paperwork and unnecessary movements.
In safe hands with cobots
Industrial robots that work on things like welding and assembly are ordinarily kept in cages for safety reasons, due to their size, strength and speed of movement.
By contrast, cobots (short for “collaborative robots”) offer a perfect solution for processes where people and machines need to work closely together. Cobots are robotic arms with limited strength and speed of movement. In addition to being extremely nimble, they can be easily reprogrammed to learn new tasks.
[https://flixel.com/cinemagraph/31f0l3z9tstpir5wq8x9]
At its Oppama vehicle assembly plant (shown above) and Yokohama powertrain plant, Nissan uses Universal Robots’ UR-10 cobots for multiple processes requiring frequent lifting or repetitive motions, such as loosening bolts or carrying engine components.
Miyako Shiraishi, a production engineer at the Yokohama Plant, says there were several reasons for choosing cobots over conventional robots.
“They can share the workspace with workers, we can build systems without needing safety fences, and we can move them around easily to adapt to changes in our production needs,” Shiraishi explains.
Karakuri: old-school automation
Karakuri is a Japanese word for devices that use mechanical gadgetry – rather than electronics, hydraulics or pneumatics – to accomplish a task. The name originally comes from a centuries-old tradition of mechanical puppetry in Japan.
Karakuri involves clever and inherently eco-friendly solutions to practical problems often involving hooks, pulleys and counterweights to perform tasks. Carmakers use karakuri to transport objects over long distances or to ensure that the right parts for any given process are automatically delivered to workers, making tasks easier and more efficient.
[https://flixel.com/cinemagraph/s6psq5dlx0745gpj1c9e]
All Nissan plants use karakuri of various shapes and sizes. The company’s engineers are constantly experimenting by developing and testing new devices. For engineers, dreaming up karakuri is a logical and creative exercise, and the devices can cut costs and improve productivity while simultaneously eliminating menial work and preventing mistakes.
Exoskeletons can help shoulder the burden
Another example of devices that ease the burden on workers are the exoskeleton devices being tested at Nissan’s Barcelona Plant. This innovation has shown a significant potential to enhance the strength and stamina of workers.
[https://flixel.com/cinemagraph/b1shlmr5tq326mnddp8o]
The exoskeletons are lightweight (1.5 to 3 kilograms) and offer shoulder and arm support for workers performing particularly strenuous overhead tasks. At the Barcelona Plant, they’ve been shown to reduce muscle strain by up to 60%.
Nissan uses a lot of additional techniques to lighten the load on workers. In some plants, workers sit on “ergo-chairs” attached to robot arms, letting them enter vehicle cabins quickly and effortlessly. In some cases, Nissan has even redesigned vehicles themselves to make them easier for workers to build.
All of these initiatives are based on Nissan’s firm belief that the cars of the future, no matter how complex, must be built by humans. Technological advances and creative engineering solutions are now allowing us to ensure that our workers are performing to the best of their ability, and that the burden of their work is minimized.
To learn more about Nissan’s exoskeleton trial, visit https://www.youtube.com/watch?v=nJe3ZFv3Cyg.
More info about the UR-10 cobots at Nissan’s Yokohama Plant can be found at https://www.universal-robots.com/case-stories/nissan-motor-company/.